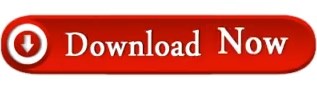
The most significant disruptors in pharma operations have been and will continue to be new product modalities (such as cell and gene therapy), digitization, and advanced analytics. What are the best practices to fill skill gaps?.What specific roles and skills will be required in the future?.How do executives and frontline personnel perceive these workforce changes?.What impact from these trends will frontline personnel feel (by role) and when?.More than 3,700 respondents from 28 countries completed the surveys, which focused on several key questions: McKinsey did the primary research by surveying executives and frontline personnel at 17 pharmaceutical manufacturers and pharmaceutical-engineering companies.
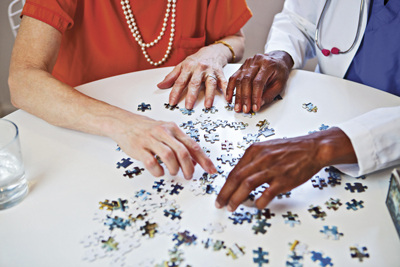
The International Society for Pharmaceutical Engineering (ISPE) and McKinsey collaborated to understand the major trends shaping the workforce of the future in pharma operations. Pharma companies have been slow to address talent gaps In pharma specifically, the new industry models aim to improve the patient experience and outcomes. Technology also creates new jobs and income possibilities-although demand for manual and physical labor is decreasing, demand for socioemotional and technological skills is growing.
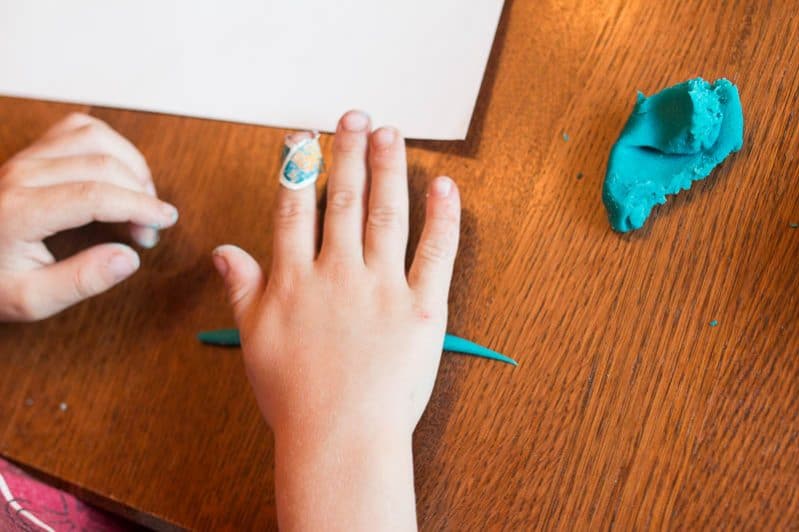
Across industries, technological shifts promise more efficient and effective operations for example, labor markets can use digital talent platforms to match workers with jobs. Yet they could have a positive impact on patients, employees, and manufacturers. Such changes, which affect not only the supply and demand of labor but also job profiles, often lead to public tensions. Over the next decade, pharma executives expect an annual increase of 27 percent in the percentage of roles affected. Jobs lost, jobs gained: What the future of work will mean for jobs, skills, and wages, November 2017, McKinsey Global Institute. In ten years, more than 90,000 jobs could disappear, while a different set of 90,000 to 120,000 jobs may be created. Even now, an estimated 50 percent of existing work activities in the pharmaceutical- and medical-manufacturing industry could be automated. Occupational profiles are changing too: some jobs are disappearing as a result of automation while entirely new jobs are emerging. These macro trends are generating major shifts in the skills the operations workforce must have and forcing companies and their employees to accept new ways of working. Pharma is also facing its own disruptions-for example, new business models (such as direct-to-customer sales and personalized medicine) and new product modalities (for instance, cell and gene therapy). Manufacturers are introducing advanced technologies, automating and digitizing processes, and applying advanced analytics to data. The unprecedented pace and scale of technological disruption brought on by the fourth industrial revolution is affecting the operations function across all industries. However, we believe there is ample evidence that it is changing dramatically. In a world experiencing unprecedented technological change, have pharma operations been left behind or are they participating in the radical advances? Some might argue that the industry has been stagnant, with little transformative change over the past 50-plus years: a tablet-compression machine today looks a lot like one from the 1950s, microbiologists and chemists run many lab tests in the same old ways, and the industry continues to face challenges in using data to draw meaningful insights.
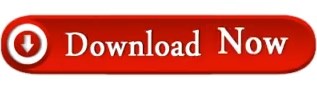